Das Buch, das das Leben und die Karriere des aktuellen CEO von Apple, Tim Cook, beschreibt, wird in wenigen Tagen veröffentlicht. Sein Autor, Leander Kahney, teilte dem Magazin Auszüge daraus mit Kult des Mac. In seinem Werk beschäftigte er sich unter anderem mit Cooks Vorgänger Steve Jobs – die heutige Auswahl beschreibt, wie sich Jobs im fernen Japan inspirieren ließ, als er die Macintosh-Fabrik gründete.
Inspiration aus Japan
Steve Jobs war schon immer von automatisierten Fabriken fasziniert. Er begegnete dieser Art von Unternehmen erstmals 1983 auf einer Reise nach Japan. Damals hatte Apple gerade seine Diskette namens Twiggy produziert, und als Jobs die Fabrik in San Jose besuchte, war er von der hohen Produktionsrate unangenehm überrascht Fehler - mehr als die Hälfte der produzierten Disketten war unbrauchbar.
Jobs könnten entweder die meisten Mitarbeiter entlassen oder sich anderswo nach Produktionsmöglichkeiten umsehen. Die Alternative war ein 3,5-Zoll-Laufwerk von Sony, hergestellt von einem kleinen japanischen Zulieferer namens Alps Electronics. Der Schritt erwies sich als richtig, und nach vierzig Jahren ist Alps Electronics immer noch Teil der Lieferkette von Apple. Steve Jobs traf Yasuyuki Hiroso, einen Ingenieur bei Alps Electronics, auf der West Coast Computer Faire. Laut Hirose interessierte sich Jobs vor allem für den Herstellungsprozess und während seines Rundgangs durch die Fabrik hatte er unzählige Fragen.
Neben japanischen Fabriken ließ sich Jobs auch in Amerika von Henry Ford selbst inspirieren, der ebenfalls eine Revolution in der Industrie auslöste. Ford-Autos wurden in riesigen Fabriken zusammengebaut, in denen Produktionslinien den Produktionsprozess in mehrere wiederholbare Schritte unterteilten. Das Ergebnis dieser Innovation war unter anderem die Möglichkeit, ein Auto in weniger als einer Stunde zusammenzubauen.
Perfekte Automatisierung
Als Apple im Januar 1984 seine hochautomatisierte Fabrik in Fremont, Kalifornien, eröffnete, konnte das Unternehmen einen kompletten Macintosh in nur 26 Minuten zusammenbauen. Die Fabrik am Warm Springs Boulevard war mehr als 120 Quadratmeter groß und hatte das Ziel, in einem einzigen Monat bis zu eine Million Macintosh-Computer zu produzieren. Wenn das Unternehmen über genügend Teile verfügte, lief alle XNUMX Sekunden eine neue Maschine vom Band. George Irwin, einer der Ingenieure, die an der Planung der Fabrik beteiligt waren, sagte, dass das Ziel im Laufe der Zeit sogar auf ehrgeizige dreizehn Sekunden reduziert wurde.
Jeder der damaligen Macintosh-Geräte bestand aus acht Hauptkomponenten, die einfach und schnell zusammengebaut werden konnten. Produktionsmaschinen konnten sich in der Fabrik bewegen und wurden auf speziellen Schienen von der Decke herabgelassen. Die Arbeiter hatten zweiundzwanzig Sekunden – manchmal auch weniger – Zeit, um den Maschinen bei der Erledigung ihrer Arbeit zu helfen, bevor sie zur nächsten Station weitergingen. Alles wurde detailliert berechnet. Apple konnte zudem sicherstellen, dass die Arbeiter nicht über eine Entfernung von mehr als 33 Zentimetern zu den benötigten Bauteilen greifen mussten. Der Transport der Bauteile zu den einzelnen Arbeitsplätzen erfolgte mit einem automatisierten Lkw.
Die Montage der Computer-Motherboards wiederum wurde von speziellen automatisierten Maschinen übernommen, die Schaltkreise und Module auf den Platinen befestigten. Apple-II- und Apple-III-Computer dienten meist als Terminals, die für die Verarbeitung der notwendigen Daten verantwortlich waren.
Streit um Farbe
Zunächst bestand Steve Jobs darauf, dass die Maschinen in den Fabriken in den Farbtönen lackiert werden sollten, auf die das Firmenlogo damals stolz war. Doch das war nicht machbar, also griff Werksleiter Matt Carter auf das übliche Beige zurück. Aber Jobs beharrte auf seiner charakteristischen Sturheit, bis eine der teuersten Maschinen, leuchtend blau lackiert, aufgrund der Farbe nicht mehr ordnungsgemäß funktionierte. Am Ende ging Carter – die Auseinandersetzungen mit Jobs, bei denen es auch oft um absolute Kleinigkeiten ging, waren nach seinen eigenen Worten sehr anstrengend. Carter wurde durch Debi Coleman ersetzt, eine Finanzbeamtin, die unter anderem die jährliche Auszeichnung für den Mitarbeiter gewann, der Jobs am meisten zur Seite stand.
Doch auch sie wich dem Streit um die Farben in der Fabrik nicht aus. Diesmal war es Steve Jobs, der darum bat, die Wände der Fabrik weiß zu streichen. Debi argumentierte mit der Umweltverschmutzung, die durch den Betrieb der Fabrik sehr bald eintreten würde. Ebenso bestand er auf absolute Sauberkeit in der Fabrik – damit „man vom Boden essen kann“.
Minimaler menschlicher Faktor
Nur sehr wenige Prozesse in der Fabrik erforderten die Arbeit von Menschenhand. Die Maschinen konnten mehr als 90 % des Produktionsprozesses zuverlässig abwickeln, wobei die Mitarbeiter vor allem dann eingriffen, wenn es darum ging, einen Defekt zu beheben oder fehlerhafte Teile auszutauschen. Auch Aufgaben wie das Polieren des Apple-Logos auf Computergehäusen erforderten menschliches Eingreifen.
Der Betrieb umfasste auch einen Testprozess, den sogenannten „Burn-In-Zyklus“. Dies bestand darin, jede der Maschinen mehr als vierundzwanzig Stunden lang jede Stunde aus- und wieder einzuschalten. Das Ziel dieses Prozesses bestand darin, sicherzustellen, dass jeder Prozessor ordnungsgemäß funktionierte. „Andere Unternehmen schalteten einfach den Computer ein und beließen es dabei“, erinnert sich Sam Khoo, der als Produktionsleiter vor Ort tätig war, und fügt hinzu, dass das genannte Verfahren fehlerhafte Bauteile zuverlässig und vor allem rechtzeitig erkennen könne.
Die Macintosh-Fabrik wurde von vielen als die Fabrik der Zukunft beschrieben, die Automatisierung im wahrsten Sinne des Wortes darstellt.
Leander Kahneys Buch „Tim Cook: The Genius who take Apple to the Next Level“ erscheint am 16. April.
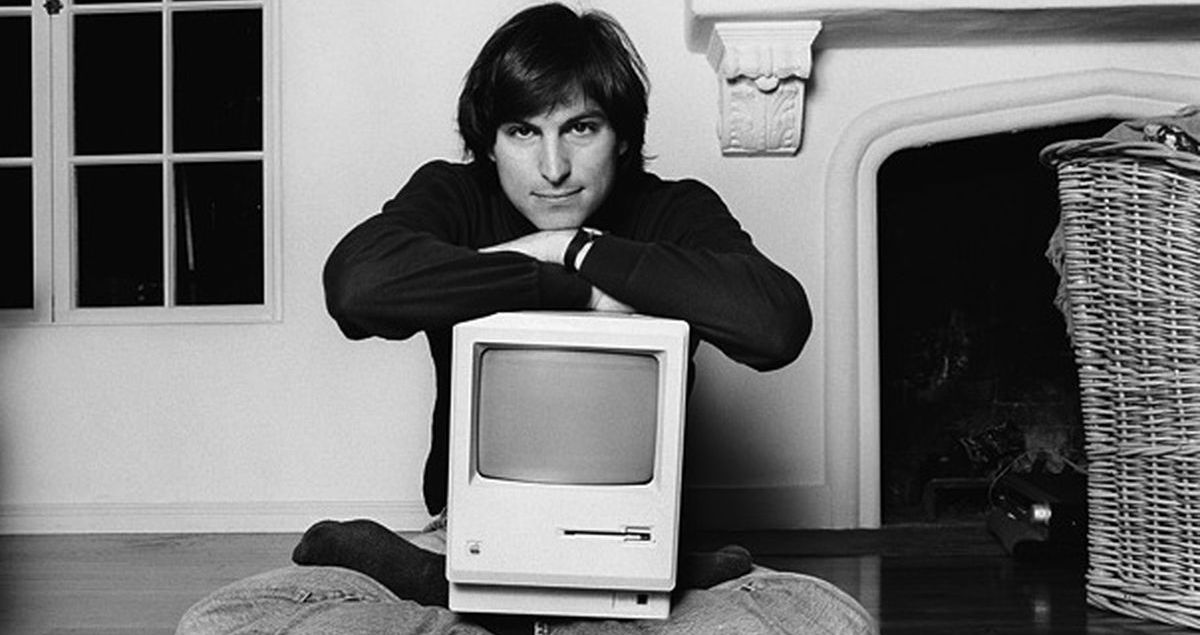
Eine Fabrik mit einer Fläche von über 120 Quadratmetern … Hmmm, ich weiß, dass es dieses magische „mehr als“ gibt, also könnten es etwa 120 sein. Quadratmeter, aber immer noch. Es musste nicht nur eine hochautomatisierte, sondern auch eine stark miniaturisierte Fabrik sein. :-)